Certification & Approval
Having worked out a promising-looking layout, initial three-view and performance and weight specifications, now is the stage where the hard work begins of transforming concepts to working drawings. Essential decisions have to be made about types of material to be used, the structural arrangement, exact choice of powerplant and so on. You’ll probably need to make a cockpit mock-up to check the ergonomics and control system arrangements, and maybe build a flying radio controlled model of the design to give faith in the handling characteristics.
With the basic geometry laid out, stress calculations and assembly drawings come next, then drawings of individual piece parts. Keep an up-to-date tally on weights. As the drawings get more detailed you must re-evaluate whether you are going to meet your original targets in terms of weight, strength and aerodynamic cleanliness, whether you need to re-visit your original assumptions or re-design from scratch. Is there a way that the part or assembly can be made more easily, more cheaply, lighter, stronger, more fatigue or corrosion resistant ? Fewer parts and fewer joints generally means fewer problems and less weight. Can you use off the shelf parts rather than having to make them specially ? Are there other aeroplanes around that have already solved a particular problem in a clever way ? Will the aircraft be easy to inspect in service, easy to repair if it gets damaged ? Can it be broken down for transportation ? If the handling isn’t quite right when the prototype is test flown, does the design make provision for ‘tweaks’ to put it right ? Does the design include reserves of strength to cope with weight growth in service and more powerful engines, or is everything pared down to the minimum ?
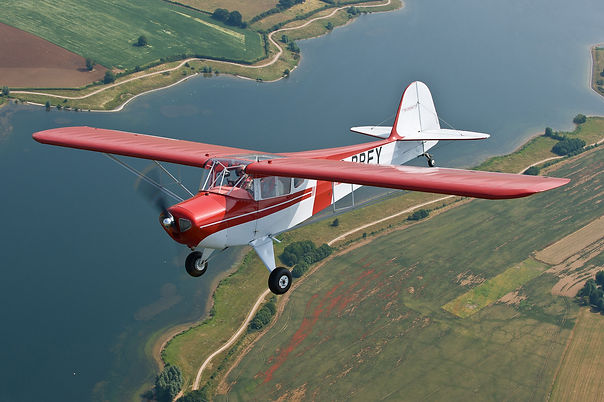